Voordat we in de geschiedenis van Lean en Six Sigma duiken…
De geschiedenis van Lean wordt vaak herleid naar de Japanse autofabriek van Toyota, wat na de Tweede Wereldoorlog langzaam steeds succesvoller werd. Hoewel het een leuke aanname is dat Lean hier zijn echte oorsprong vond, zijn we er inmiddels achter dat Lean al eerder in de geschiedenis bestond. Alleen zal deze methode toen niet deze naam hebben gehad. Sommige mensen beweren zelfs dat de oude Egyptenaren dergelijke denkwijzen gebruikten om al die gigantische stenen te gebruiken voor de bouw van piramides. Zoals je vaker op deze website zult lezen, gaat het bij Lean niet om harder werken, maar juist om slimmer werken. Hierboven staat een tijdlijn weergegeven. De geschiedenis van Lean en Six Sigma is onderverdeeld in drie tijdvakken. U kunt gebruik maken van de balk om naar het gewenste tijdvak te springen, of alles op volgorde lezen door naar beneden te scrollen.
1799 – 1947
Waar de gedocumenteerde geschiedenis van Lean en Six Sigma begon
Ontwikkelingen in het Westen
Lean staat bekend om haar modulaire opbouw. Dit betekent dat de verschillende onderdelen van het systeem uitwisselbaar zijn. Zo’n systeem wordt in de volksmond ook wel een bouwdoossysteem genoemd. Het doel hiervan is om gemakkelijk producten te bouwen maar ook onderdelen te vervangen, waar nodig. Dit principe komt bij Eli Whitney vandaan, die in 1799 het concept van de ‘interchangeable parts’ introduceerde. Interchangeable betekent ook hier uitwisselbaar. Een aantal personen die tijdens de Industriële Revolutie veel hebben bijgedragen aan Lean staan hieronder weergegeven. Klik op hun namen om meer te weten te komen over wie ze waren en wat hun bijdrage is geweest.
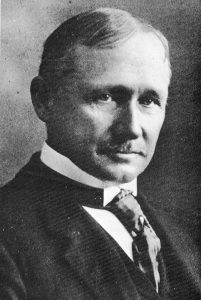
Gedurende de Industriële Revolutie werd massaproductie een standaard. Frederick Taylor hield zich gedurende die tijd bezig met arbeidsverdeling en hoe dit geoptimaliseerd kon worden. Deze manier van management noemen we ook wel Scientific Management. Hij onderzocht het organiseren van werk en de taken binnen dat werk. Vooral zijn shop management werk in 1903 was enorm vernieuwend. Het zal je niet verbazen dat fabrieken als wortels uit de grond kwamen zetten. Deze manier van massaproductie was immers een geweldige manier om producten te fabriceren. Echter was niet alles even handig geregeld. De opkomst van al die fabrieken nam ook de nodige interne fouten met zich mee. Daarom heeft hij samen met Frank en Lilian Gilbreth gezorgd voor nieuwe inzichten over hoe je besluiten neemt op basis van feiten in plaats van gevoel, en hoe je hiermee dan vervolgens een proces organiseert. Een voorbeeld hiervan zijn de ‘Time and Motion Studies’.
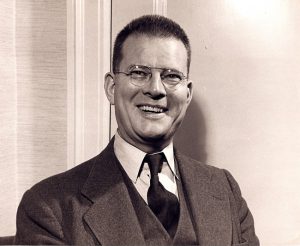
William Edwards Deming was een leerling van Walter Shewhart en hielp na de Tweede Wereldoorlog in Japan met de wederopbouw door het delen van inzichten over Statistische Proces Controle (SPC) en het wegnemen van verspillingen. Hij behoort samen met Crosby en Juran tot de kwaliteitsgoeroes. We kennen Deming van de Deming Circle. Deze bestaat uit: Plan, Do, Check, Act (PDCA) of Plan, Do, Study, Act (PDSA). Ook staat deming bekend om de 14 punten waarmee elke organisatie kan groeien. Deze 14 punten zijn: 1. Creëer een solide doelstelling voor verbetering van producten en diensten.2. Neem de nieuwe filosofie in u op. Wij bevinden ons in een nieuw economisch tijdperk. Westers management moet de uitdaging oppakken.3. Om kwaliteit te bereiken, moet u niet meer afhankelijk zijn van inspecties.4. Stop met de praktijk van belonen op basis van het prijskaartje. Minimaliseer in plaats daarvan de totale kosten.5. Verbeter voortdurend en altijd het systeem van productie en dienstverlening teneinde de kwaliteit en de productiviteit te verbeteren en daardoor de kosten te verlagen en de winst te verhogen.6. Voer training tijdens het werk in.7. Voer leiderschap in. Het doel van leiderschap dient te zijn: mensen en machines te helpen beter te presteren.8. Verdrijf angst, zodat iedereen doelmatig voor de onderneming kan werken.9. Breek de grenzen tussen afdelingen af. Optimaliseer de onderneming als systeem.10. Stop met slagzinnen, aansporingen en doelen voor de medewerkers.11. (a) Verwijder de normen (quota) voor het werk.
(b) Schrap het Management by Objectives. Schrap het sturen op basis van aantallen en cijfermatige doelen.12. (a) Verwijder de hindernissen die de ambachtsman beroven van zijn recht om trots te zijn op zijn vakmanschap.
(b) Verwijder de hindernissen die mensen in management en op de werkvloer in de weg staan van hun recht op trots te zijn op hun vakmanschap. Dit betekent, tussen haakjes, de afschaffing van de jaarlijkse beoordeling.13. Voer een daadkrachtig programma voor opleiding en zelfontwikkeling in.14. Laat iedereen in de onderneming werken aan het realiseren van deze transformatie.
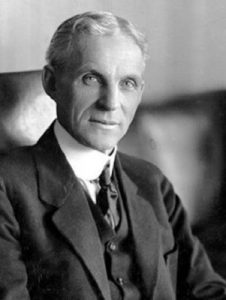
Oprichter van de Ford Motor Company (1903), nu beter bekend als Ford.
Hij bracht de organisatie van efficiënte productie tot een hoger niveau door de lopende band in zijn fabriek te introduceren in 1908. Hierdoor werd de T-Ford de meest gewilde automobiel van zijn tijd. Uiteindelijk verloor Ford zijn populariteit een tijdje door een tekort aan keuzemogelijkheden voor de klant
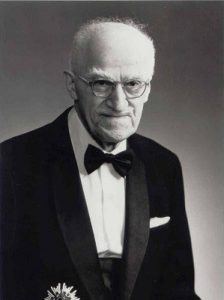
Juran behoort samen met Crosby en Deming tot de kwaliteitsgoeroes. Juran is bekend om de kwaliteitstrilogie, namelijk Quality Control, Quality Planning en Quality Improvement. Juran legde daarbij de aandacht op kwaliteitskosten (Cost-of-Poor-Quality). Kwaliteitskosten kunnen worden onderverdeeld in drie groepen: Preventiekosten, Beoordelingskosten en Faalkosten.
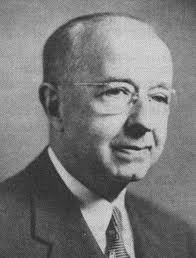
Walter Shewhart werkte aan een opdracht om het aantal gemaakte fouten in fabrieken terug te dringen. Dit zou er op zijn beurt voor zorgen dat er minder producten terug werden gebracht naar de fabriek. Shewhart kwam erachter dat ieder proces natuurlijke variantie bevat. Vergelijk het maar met het lezen van een tijdschrift. De gemiddelde tijd die je gebruikt om een bladzijde te lezen is wellicht drie minuten, maar als je per bladzijde gaat meten, dan zal je merken dat je zo nu en dan onder die drie minuten zit en op andere momenten erboven. Zo werkt het met processen ook. De gemiddelde productietijd zegt ons niet zoveel, want ieder individueel proces loopt altijd net weer een beetje anders qua tijd.
In een proces kan ook sprake zijn van niet-natuurlijke variantie. In dat geval zeggen we dat het proces niet in controle is. Je kan er achter komen of er variantie
in een proces zit door middel van een Statistische Proces Controle (SPC).
Ontwikkelingen in Japan
In Japan werd er door Sakichi Toyoda gezorgd voor een nieuwe vondst. Deze man was niet alleen de oprichter van Toyota, maar ook een uitvinder. Hij bedacht een methode waardoor een machine automatisch afslaat als er een fout is. Dit principe kennen we als Jidoka. Zijn zoon was verantwoordelijk voor het principe van Just-in-Time. Oftewel pas als het materiaal moet worden verwerkt, voer je het aan. Taiichi Ohno bracht alle best practices samen wat resulteerde in het Toyota Productie Systeem, waarover je verder op de pagina meer kan lezen.
William Deming en Joseph Juran hebben in de wederopbouw van de Japanse economie hun inzichten gedeeld. Japan had daarvoor de Japanese Union of Engineers en Scientist (JUSE) opgericht. Het doel van de JUSE was om de Japanse economie niet alleen weer op te bouwen maar vooral nieuwe inzichten te geven om uiteindelijk de standaard te worden voor manufacturing. In het Westen werd men zich bewust van de kracht van deze inzichten, toen Japan niet alleen veel goedkoper maar vooral ook veel betere producten produceerde dan het Westen. Een deel was te wijten aan de lagere loonkosten, maar dat bleek niet de echte doorslaggevende factor. Het zat hem vooral in een andere manier van werken. Die manier van werken is wat we in de hedendaagse tijd kennen als Lean.
Kiichiro Toyoda wordt beschouwd als de geestelijk vader van Just-in-Time, later geperfectioneerd door Taiichi Ohno. Zelf zei hij erover in 1938 in een interview met een journalist: “I believe that the most important thing is to ensure that there is neither shortage nor excess, that is, to ensure that there is no excess labor and time for the designated production. There is no waste and there is no excess. It means not having to wait for parts to be circulated around. For Just-in-Time, it is important that each part be ready ‘just in time’. This is the first principle of increasing efficiency”.
- You are a cost. First reduce waste.
- First say, “I can do it.” And try before everything.
- The workplace is a teacher. You can find answers only in the workplace.
- Do anything immediately. Starting something right now is the only way to win.
- Once you start something, persevere with it. Do not give up until you finish it.
- Explain difficult things in an easy-to-understand manner. Repeat things that are easy to understand.
- Waste is hidden. Do not hide it. Make problems visible.
- Valueless motions are equal to shortening one’s life.
- Re-improve what was improved for further improvement.
- Wisdom is given equally to everybody. The point is whether one can exercise it.
Lean als gevolg van kwaliteitsmanagement
De basis voor de Statistische Proces Controle werd verder uitgewerkt in samenhang met andere principes voor kwaliteitsmanagement door zowel Deming als Juran. Zij hebben beide in de wederopbouw van de Japanse economie geholpen en hun inzichten gedeeld. Japan richtte vervolgens de Japanese Union of Engineers en Scientist (JUSE) op. Dit had als doel om niet alleen de Japanse Economie weer op te bouwen, maar ook om ze nieuwe inzichten te bieden.
In het westen werd het nut en de kracht van deze inzichten ingezien toen Japan in de jaren ’80 niet alleen goedkoper ging produceren, maar ook nog eens een betere kwaliteit producten produceerde. Dit was voornamelijk bereikt door een andere manier van werken en een andere benadering qua productie en management. Dit kennen we vandaag als het begrip: LeaKaoru Ishikawa.
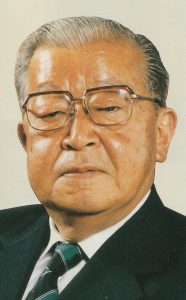
- Bepaal doelen en doelen.
- Bepaal methoden om de doelen te bereiken.
- Neem deel aan onderwijs en training.
- Voer het werk uit.
- Controleer de effecten van de implementatie.
- Neem passende maatregelen.
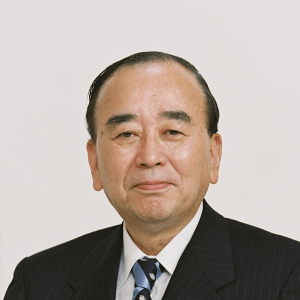
1947 – 2000
Het Toyota Productie Systeem en de origine van Six Sigma
Het Toyota Productie Systeem
Toyota was zich wel bewust van de grote concurrenten in Amerika. Daar ging het momenteel beter, omdat die veel meer resources en schaalvoordelen hadden. Toyota besloot zich juist te concentreren op het elimineren van waste en juist flexibel te zijn, iets wat de grote concurrenten niet waren. Wie niet sterk is, moet slim zijn! Ohno was de architect van het hele systeem van waste elimineren en ervoor zorgen dat je je concentreert op de individuele stuks in plaats van de massa. Hij werd hierin ondersteund door Shingeo Shingo, die zich bezighield met het bereiken van maximale flexibiliteit in de productielijn. Mensen staan centraal in dit productie Systeem van Toyota. Dat wil zeggen dat de mensen daadwerkelijk de waarde toevoegen aan het proces en zelf de mogelijkheid tot verbeteren hebben. Op de pagina, die hieronder te zien is gaan we dieper in op het Toyota Productie Systeem.
Meer weten over het Toyota Productie Systeem, hoe het tot stand is gekomen en hoe het exact is opgebouwd? Klik op de button hieronder en neem een kijkje op deze pagina, waar we hier uitgebreid op in gaan!
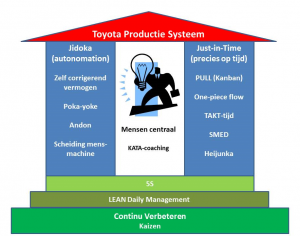
Six Sigma
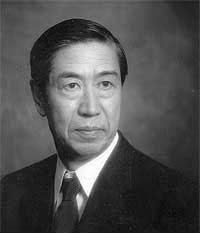

- kwaliteit is voldoen aan de eisen
- voorkomen is het doel van een kwaliteitssysteem
- de norm is nul defecten ten opzichte van de eisen
- kwaliteit kan worden uitgedrukt door de prijs van non-conformiteit
Motorola en Six Sigma
Bij Motorola was men in de jaren ’80 bezig met een kwaliteitsprogramma. Het doel van dit programma was om per 1 miljoen kansen twee fouten toe te staan. Uiteindelijk werd dit aangepast naar 3,4 fouten per 1 miljoen kansen. Het programma waar ze mee bezig waren heette Six Sigma.
Jack Welch was de charismatische bestuursvoorzitter van General Electric (GE) van 1981 tot 2001 waar Six Sigma als kwaliteitsstrategie werd ingezet. De zogenaamde key concepts zoals die bij GE worden toegepast zijn:
– Critical to Quality: Attributes most important to the customer;
– Defect: Failing to deliver what the customer wants;
– Process Capability: What your process can deliver;
– Variation: What the customer sees and feels
– Stable Operations: Ensuring consistent, predictable processes to improve what the customer sees and feels;
– Design for Six Sigma: Designing to meet customer needs and process capability.
2000 – heden
Waar we de geschiedenis van Lean en Six Sigma doorgeven
De doorontwikkeling van Lean
Eenmaal in de 21e eeuw, na vele succesverhalen en de eenvoud van de methode, namen de Lean implementaties steeds meer toe. Hoewel de focus eerst puur lag op de industrie is dit inmiddels enorm uitgebreid. Er is in 2020 geen enkele sector meer die nog niet in aanraking is geweest met Lean. Veel onderzoeken bevestigen de toepasbaarheid van Lean, maar er zijn echter ook verhalen van mislukte implementaties. In onderzoeken na 2000 werd ook steeds duidelijk dat Lean niet alleen een tool is die je toepast, maar dat het een manier van denken is. Volgens sommigen kan je Lean zelfs zien als een filosofie die de gehele organisatie raakt en diep ingaat op hoe je jezelf en de werkvloer organiseert. Lean moet je dan ook vooral zien als een systeem benadering die verder gaat dan wat tools toepassen.